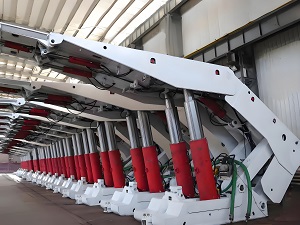
一、液压支架磨损修复的行业痛点
在煤矿机械领域,液压支架长期承受高压冲击和矿石摩擦,立柱、顶梁等关键部件易产生严重磨损。采用堆焊技术修复时,既要保证焊缝硬度(通常需达到HRC45-60范围),又要避免因硬度过高导致的开裂风险。耐磨焊丝的合理选型与工艺控制成为技术核心。在本文内容中,将探讨如何运用耐磨焊丝在堆焊液压支架时进行有效的硬度控制。
二、耐磨焊丝的选择
1.根据工况需求选焊丝:
不同煤矿开采环境下,液压支架面临的磨损形式各异。在高磨粒磨损工况中,如刮板输送机频繁刮擦的区域,应选用含有高硬度碳化物颗粒的耐磨焊丝,像碳化钨合金焊丝,其碳化钨颗粒能有效抵御磨粒的切削,显著提高堆焊层的耐磨性,进而提升硬度。对于既有磨损又有腐蚀的环境,可选择含铬、镍等合金元素的不锈钢耐磨焊丝,如常见的LQ357Z耐磨焊丝,铬元素能增强耐腐蚀性,镍元素则有助于提高堆焊层的韧性和强度,在抵抗腐蚀的同时保证一定的硬度。
2.匹配母材的重要性:
液压支架母材的材质是选择耐磨焊丝的关键依据之一。若母材为低合金钢,应挑选成分与母材相近、热膨胀系数匹配的耐磨焊丝,以确保堆焊层与母材能良好融合,减少焊接缺陷,避免因热应力导致堆焊层硬度不均匀或出现裂纹。例如,雷公LQ370Z焊丝常用于低合金钢母材的堆焊,能在保证硬度的同时,确保堆焊层与母材的结合强度。
三、焊接工艺参数的优化
1.焊接电流与电压的调控:
焊接电流和电压直接影响堆焊层的熔深、熔宽以及稀释率,进而对硬度产生显著影响。一般来说,增加焊接电流会使熔深增大,母材稀释率提高,可能导致堆焊层硬度下降;而电压过高则会使电弧不稳定,出现飞溅,影响堆焊层的成型和硬度均匀性。以二氧化碳气体保护焊为例,在堆焊液压支架时,电压通常控制在 22 - 26V 之间。在实际操作中,需根据焊丝材质、母材厚度以及现场焊接条件进行微调,通过试焊确定最佳参数组合,以保证堆焊层硬度符合要求。
2.焊接速度的影响:
焊接速度与焊接电流、电压相互关联,共同决定焊接线能量。过快的焊接速度会使熔池冷却速度过快,导致堆焊层结晶组织粗大,硬度降低且不均匀;过慢的焊接速度则会使焊接线能量过大,母材稀释率增加,同样影响堆焊层硬度。通常,焊接速度保持在 30 - 50cm/min 较为合适。在实际堆焊过程中,要根据焊接设备的性能和操作熟练程度,合理调整焊接速度,确保堆焊层硬度稳定。
四、焊前与焊后处理
1.焊前预热:
焊前对液压支架母材进行预热,是降低焊接应力、防止堆焊层出现裂纹、保证硬度均匀性的重要措施。预热温度需根据母材材质、厚度以及环境温度等因素确定。对于普通低合金高强度钢母材的液压支架,预热温度一般控制在 100 - 200℃(具体需结合工件的实际情况确定)。通过火焰加热、电阻加热等方式对母材进行均匀预热,可有效减少焊接过程中的温度梯度,使堆焊层在冷却过程中能均匀结晶,避免因局部应力集中导致硬度异常。
2.焊后热处理:
焊后热处理能进一步消除焊接残余应力,改善堆焊层的组织和性能,优化硬度。通过回火处理可使堆焊层中的残余奥氏体转变为稳定的组织,减少堆焊层的脆性,提高其韧性和硬度均匀性,提升综合性能。
五、焊接操作规范
1.多层多道焊的技巧:
在堆焊液压支架时,多层多道焊是常用的焊接方式。在进行多层多道焊时,要注意每层焊道的厚度和焊接顺序。每层焊道厚度不宜过厚,一般控制在 3 - 5mm,过厚会导致热量积累过多,影响堆焊层硬度和组织性能。焊接顺序应遵循合理的原则,如分段跳焊、交错焊等,以减少焊接应力和变形,保证堆焊层硬度均匀。在焊接过程中,要确保每层焊道之间的良好融合,避免出现未熔合、夹渣等缺陷,这些缺陷会降低堆焊层的硬度和强度。
2.焊接过程中的稳定性:
焊接过程中的稳定性对堆焊层硬度至关重要。操作人员要保持稳定的焊接姿势和手法,避免焊接过程中出现晃动、抖动等情况。同时,要注意保护气体的流量和纯度,确保气体保护效果良好,防止空气中的氧、氮等杂质侵入熔池,影响堆焊层的化学成分和组织,进而导致硬度波动。在使用气体保护焊时,要定期检查气体流量表和气瓶,确保气体流量稳定,气体纯度符合要求。
在使用耐磨焊丝堆焊液压支架时,从耐磨焊丝的精心选择,到焊接工艺参数的精准优化,再到焊前与焊后处理的严格执行以及规范的焊接操作,每个环节都紧密关联,共同影响着堆焊层的硬度。只有全面把控这些要点,才能实现堆焊层硬度的精准控制,提高液压支架的耐磨性能和使用寿命,为煤矿安全生产提供坚实保障。
以上内容由耐磨焊丝厂家天津雷公焊接材料有限公司编辑 咨询电话:18202593233
|